By Anne Turkowski, Mark Hachenski, James Nyenhuis
Digital transformation. It’s a buzzword we often hear but may not fully understand. Despite much interest in this concept, many questions remain around exactly what it is, what it means and, perhaps most importantly, where do you start?
“The biggest misconception about digital transformation is that it is an all-or-nothing proposition,” says Mark Hachenski, director of digital solutions for the power and water industries. “And nothing could be further from the truth.”
It’s helpful to think of digital transformation as a journey, where each small step can lead to tangible benefits—improved performance, O&M savings, better reliability and more flexibility. One approach is to explore the digital transformation roadmap and its role in evolving toward a future with autonomous operations.
Leveraging proven software and technologies—such as wireless solutions, digital twin simulation, advanced control applications and data analytics—can have game-changing impacts on everyday operations. A closer look reveals this in more detail.
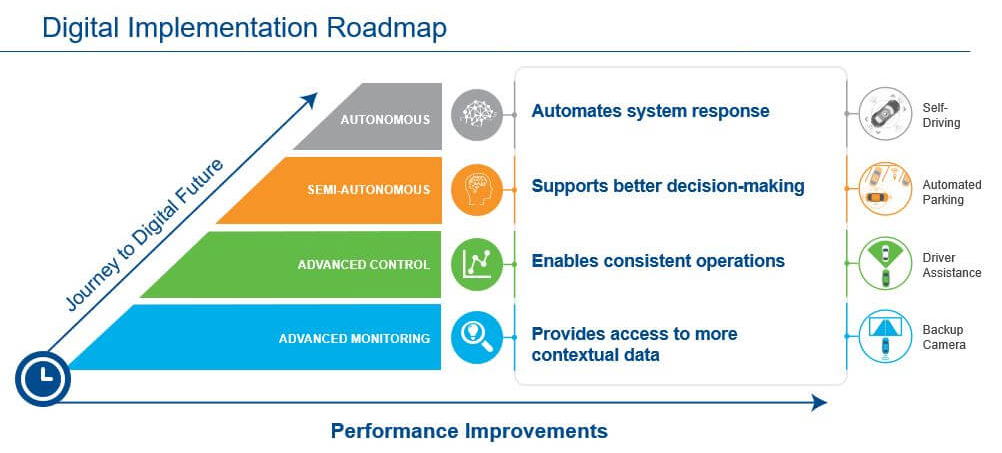
Advanced Monitoring
Outfitting equipment with wireless sensors and modern data network architecture provides greater insight into asset health and performance.
It also makes it possible to automate manual rounds, which can be a game-changer as it improves operator safety, reduces unplanned equipment breakdowns and frees up highly trained operators to spend more time performing high-value tasks, such as data analysis. In most cases, automating manual rounds pays for itself in less than a year.
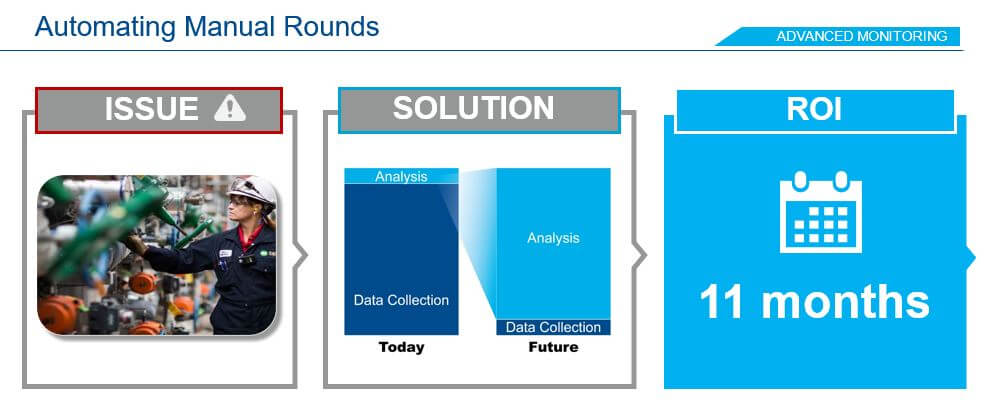
Advanced Control
In today’s environment, units are typically ramping up and down more frequently in response to system demand fluctuations, according to Jim Nyenhuis, manager of performance consulting for the power industry.
“Advanced control enables plants to ramp to setpoint more quickly and precisely, supporting grid operations and providing opportunities for additional revenue,” he explains.
These saving are so significant, most utilities realize a return on investment in less than a year.
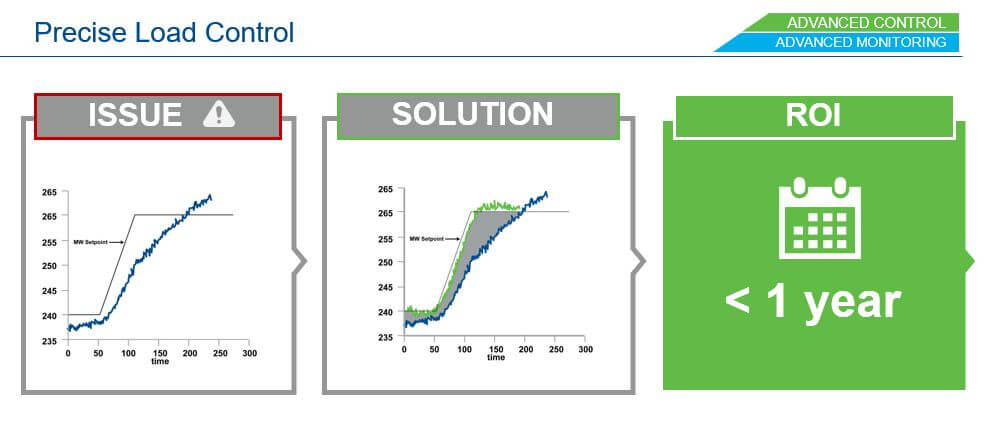
Semi-Autonomous
In the initial stages of an optimization project, historical process data is collected and used to generate models of the plant’s current operating performance to identify opportunities for improvement. Based on this information, dynamic performance metrics that are the basis for tracking and validating improvements throughout the project are developed and deployed. Once the optimized startup process is validated through analysis and testing, the focus turns to reducing variability through increased task automation and reduced dependency on manual operator intervention.
As indicated by the black dots in the illustration (below), procedural integration helps ensure consistency and paves the way for semi-autonomous startup and savings of approximately $300,000 per year.
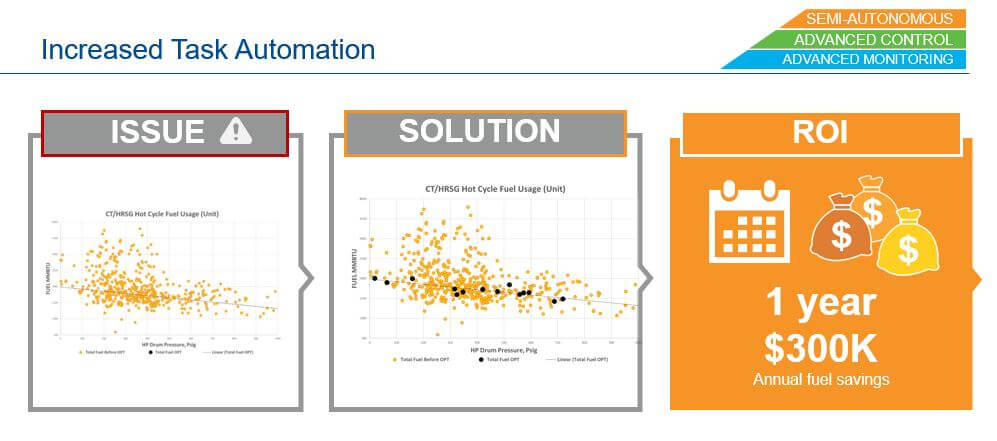
Autonomous
Remote Operations Control Centers
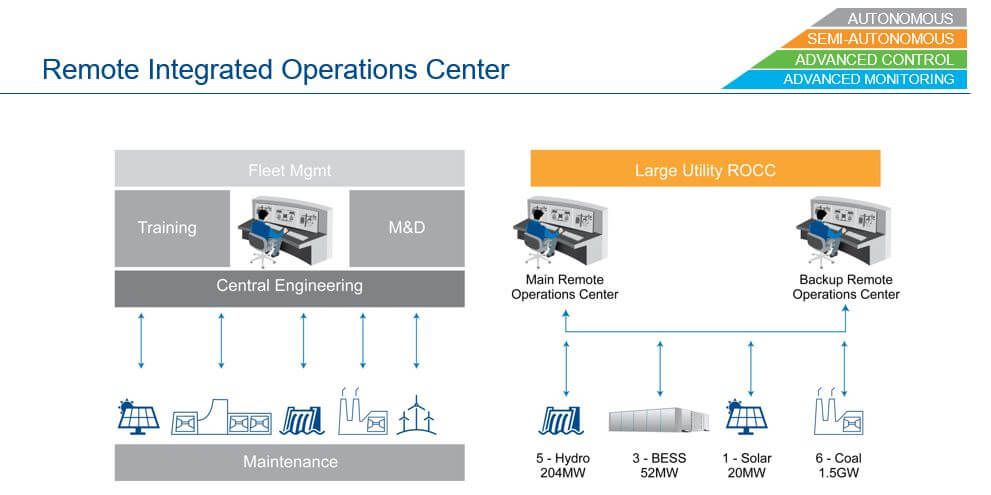
Beginning the Journey
“Collaborating with the right partner can help provide clarity and a path forward,” explains Nyenhuis. “Leveraging proven software and technologies—such as wireless solutions, digital twin simulation, advanced control applications and data analytics—can have game-changing impacts on everyday operations.”
You can learn more about how power producers can confidently take small data-driven steps that quickly deliver ROI by watching an on-demand POWER webinar featuring Emerson’s Hachenski and Nyenhuis, and moderated by POWER Magazine’s executive editor, Aaron Larson. Visit the Power Industry page on Emerson.com for more on the technologies and solutions to help drive digital transformation. And don’t forget to comment below to share your stories of your digital transformation journey!