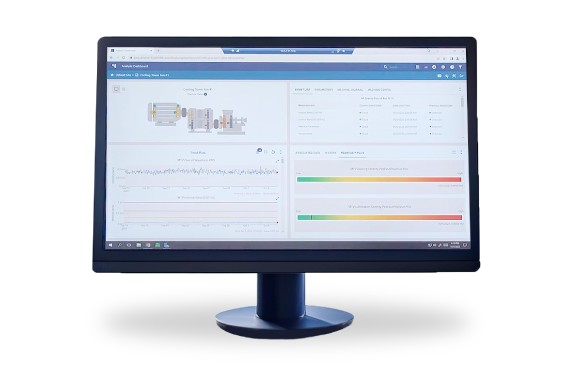
BY DEREK PINTO, SENIOR ACCOUNT MANAGER, RELIABILITY
In the world of industrial maintenance, the true measure of success is tangible results, like asset uptime capacity. You should consider your own maintenance and operations plan, cost of consumables and spare parts, as well as downtime—both planned and unplanned. Staying in the realm of conservative, estimate your own site’s operation costs and then tell me… how much would a 50% increase in asset uptime capacity yield?
When TIM (Time Interval Maintenance) Has Unintended Consequences
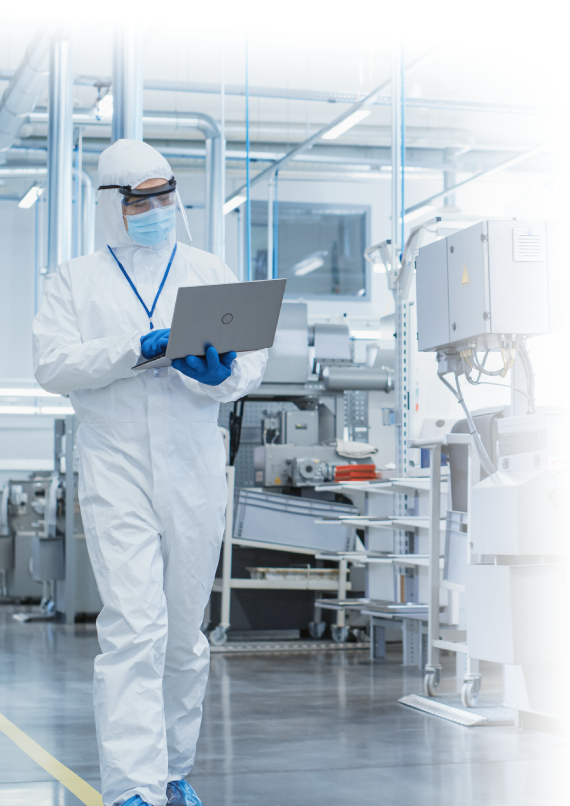
Consider a pharmaceutical manufacturer that had an exhaustive preventative maintenance (PM) program requiring that each machine train go down every 60 days for standard maintenance. This required actions like shutting down an air handling unit (AHU) that was supplying air to a clean room, so that a technician could access the enclosure to change a belt, or simply add lubrication. Seems fairly innocuous, until you realize the domino effect.
Adding lubrication to an access port on a motor is typically a 5-minute evolution, but that’s only a small portion of the total time. You must first radio the operators within those clean rooms to vacate and seal the room, then contact the HVAC team to coordinate a shutdown of a specific AHU unit, conduct your own lockout tagout activity, and finally fill out the appropriate safety information form. Then and only then, can you finally enter the enclosure to conduct your PM plan. In addition, consider the time lost on the way back to secure your lock, re-engage the AHU with coordination from the HVAC team, and finally clear the room as A-OK for the operators to return. Extrapolate this clunky series of actions over hundreds of machine trains and you realize just how much time you’re wasting to support a culture of Time-Based Maintenance.
Adding lubrication to an access port on a motor is typically a 5-minute evolution, but that’s only a small portion of the total time. You must first radio the operators within those clean rooms to vacate and seal the room, then contact the HVAC team to coordinate a shutdown of a specific AHU unit, conduct your own lockout tagout activity, and finally fill out the appropriate safety information form. Then and only then, can you finally enter the enclosure to conduct your PM plan. In addition, consider the time lost on the way back to secure your lock, re-engage the AHU with coordination from the HVAC team, and finally clear the room as A-OK for the operators to return. Extrapolate this clunky series of actions over hundreds of machine trains and you realize just how much time you’re wasting to support a culture of Time-Based Maintenance.
Cut Out the Waste & Double Uptime Capacity With PeakVue™ Plus
When this customer deployed a site-wide installation of wireless vibration monitors—1,200 sensors in all—they had a tangible goal in mind, beyond simply gaining a more robust view of their machine health. They wanted to reduce their overall PM plan by roughly 20%; however, when everything was said and done, they achieved nearly a 35% reduction in PM plan volume. Here’s how. An asset with a worn belt has a clear spectrum pattern that a trained analyst can identify. Guided by our consulting expertise and using Emerson’s Condition-Based Monitoring software, this manufacturer was able to delay those 60-day PMs until the software indicated specific signs of asset wear. Furthermore, with the software keeping an eye out for lubrication issues, as well as bearing defects, the customer began waiting for the visual cue provided by PeakVue Plus—when the green/red bar began climbing out of the green—before sending a technician out to add more lubrication.
Both of those changes, while seemingly insignificant on the surface, meant that numerous machine trains no longer had to go down every 60 days, but now every 90 to 120 days, representing a 50% to 100% increase in asset uptime capacity!
Both of those changes, while seemingly insignificant on the surface, meant that numerous machine trains no longer had to go down every 60 days, but now every 90 to 120 days, representing a 50% to 100% increase in asset uptime capacity!
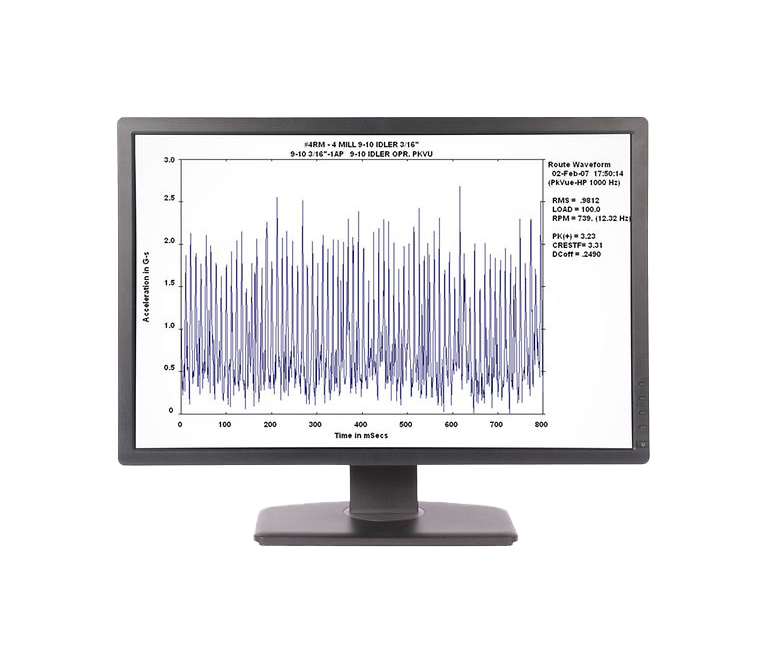
About PeakVue Plus
Emerson's PeakVue Plus is an advanced vibration analysis technology designed to enhance the monitoring and maintenance of rotating machinery. Building upon the original PeakVue technology, which focuses on detecting impacting signals indicative of developing faults in rolling element bearings, PeakVue Plus introduces prescriptive analytics to streamline the diagnostic process.
The technology’s embedded analytical algorithms automatically assess machine health, distinguishing between mechanical faults (such as bearing defects) and lubrication issues. This automation enables maintenance personnel, even those without specialized training, to make informed decisions promptly, thereby improving equipment availability and reducing unplanned downtime.
The technology’s embedded analytical algorithms automatically assess machine health, distinguishing between mechanical faults (such as bearing defects) and lubrication issues. This automation enables maintenance personnel, even those without specialized training, to make informed decisions promptly, thereby improving equipment availability and reducing unplanned downtime.