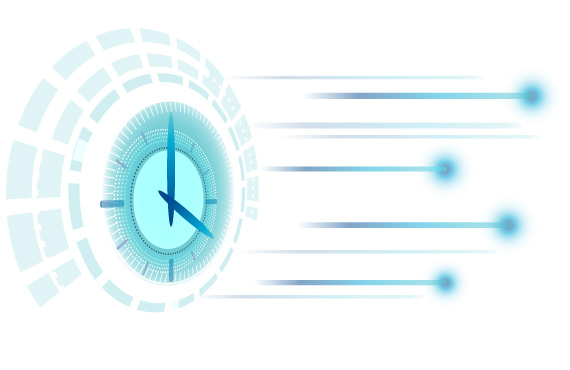
BY DEREK PINTO, SENIOR ACCOUNT MANAGER, RELIABILITY
At the crux of what I’ll call the “Reliability Movement” is a culture shift—from a traditional Time-Interval Maintenance (TIM) approach to a Condition-Based Monitoring (CBM) methodology that relies on real-time data to gain insights into the condition of an asset, as well as advanced notice of potential equipment failures.
As a proponent of Reliability, I’ve seen firsthand that predictive intelligence can determine asset health, allowing customers to reduce scheduled and unscheduled downtime, drive down maintenance costs, and increase safety and availability. From a practical standpoint, predictive diagnostics on field devices allows you to keep them configured, calibrated, and operating effectively. It’s not just my perspective; our entire industry is focused on improving reliability and certifying professionals to promote the “Reliability Cause”. For instance, SMRP is an organization devoted to advancing the maintenance, reliability and physical asset management profession. Reliabilityweb.com is another one.
TIM relies on fixed schedules, like getting the oil in your car changed regularly. While intended to be preventative, TIM can often lead to over-maintenance or missed issues that develop in between intervals (whether monthly or quarterly). There’s also cost to consider. With TIM, you’ll likely replace parts unnecessarily and also have unexpected failures—and associated downtime—between your intervals. Regardless of whether you are using your own resources or an outside firm, TIM can only identify what’s wrong at that point in time.
When I initially speak with a customer, they are most likely experiencing high volumes of preventative maintenance (with an exhaustive amount of physical labor), unplanned downtime events, high labor costs including maintenance and repairs, or all of the above. Furthermore, it seems that the more maintenance plans in place, the more they experience a nonzero chance of safety incidents. Overall, the customer is looking to maximize their asset uptime capacity and reduce labor/repair costs.
Whether for a utility, pharmaceutical manufacturer, or chemical company, Condition-Based Maintenance offers significant advantages over Time-Interval Maintenance by improving efficiency, reducing costs, enhancing safety, and providing valuable data for informed decision-making.
Specifically, the advantages of a CBM program include increased lifespan of your equipment, lower maintenance costs, proactive identification of problems, prevention of critical failures, reduced waste, and the ability to make informed decisions with real-time data.
TIM relies on fixed schedules, like getting the oil in your car changed regularly. While intended to be preventative, TIM can often lead to over-maintenance or missed issues that develop in between intervals (whether monthly or quarterly). There’s also cost to consider. With TIM, you’ll likely replace parts unnecessarily and also have unexpected failures—and associated downtime—between your intervals. Regardless of whether you are using your own resources or an outside firm, TIM can only identify what’s wrong at that point in time.
When I initially speak with a customer, they are most likely experiencing high volumes of preventative maintenance (with an exhaustive amount of physical labor), unplanned downtime events, high labor costs including maintenance and repairs, or all of the above. Furthermore, it seems that the more maintenance plans in place, the more they experience a nonzero chance of safety incidents. Overall, the customer is looking to maximize their asset uptime capacity and reduce labor/repair costs.
Customer Use Case
This chemical manufacturer recently deployed 68 AMS Wireless Vibration Monitors and PeakVue Plus technology, our prescriptive analytics software that focuses on lubrication and bearing defects. As a result, this plant was able to divert labor towards more meaningful tasks and reduce consumable spends by more than 30%, resulting in an ROI of less than 3 years.Whether for a utility, pharmaceutical manufacturer, or chemical company, Condition-Based Maintenance offers significant advantages over Time-Interval Maintenance by improving efficiency, reducing costs, enhancing safety, and providing valuable data for informed decision-making.
Specifically, the advantages of a CBM program include increased lifespan of your equipment, lower maintenance costs, proactive identification of problems, prevention of critical failures, reduced waste, and the ability to make informed decisions with real-time data.
As with any culture shift, education is the way we approach this, and as part of my next article, I’ll address the various stakeholders and their challenges/opportunities to help change their mindset. At Control Associates, where I lead the Reliability charge, we offer tiers of support and solutions, with an initial product-only option, all the way to 24/7 SME access and onsite local support. This approach, along with the appropriate information, allows the customer to walk before they run and get educated along the way.